By combining state-of-the-art fusion welding and advanced robotic laser machines with New York’s most talented engineers and machinists, you get endless possibilities for innovation in electromechanical engineering. Boyce Technologies continues to enhance our machining and manufacturing processes for greater automation and accuracy than most conventional machining centers in the United States. These advances create more innovative systems and higher quality products with quicker turnaround times for our customers.
Boyce Technologies has expanded its assortment of advanced manufacturing and laser-based production equipment to include the TRUMPF 5020 Robotic Laser Welder, the TRUMPF 3100 Trubend Hydraulic Brake, TRUMPF 2030 Trulaser Cutter, and the TRUMPF 7040 Trulaser work cell.
Advanced Robotic Welding Capabilities
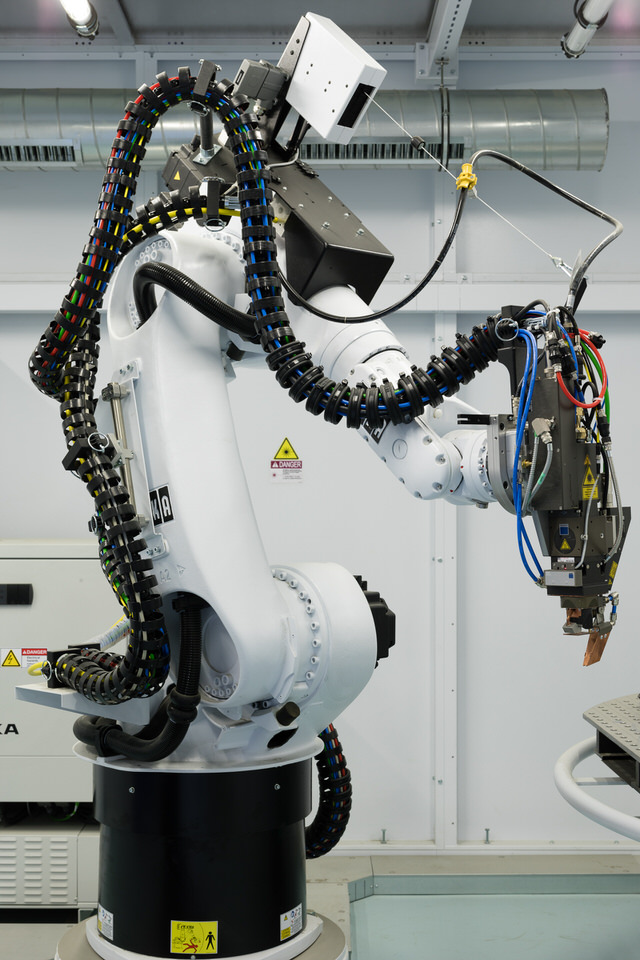
The Robotic Laser Welders are a game changer. “I’d say it is the most impressive laser equipment I’ve ever seen,” says Filippo Lavino, a Boyce Technologies Mechanical Engineer. “Laser welding has many benefits. You can weld without any filler material, which is usually required for most welding applications. You can weld two different metals together, such as copper and aluminum, which is highly desirable for heat sinks and fluid heat exchangers. You cannot do that with conventional welding because as two different metals heat up, they do not match temperatures, so it doesn’t create a good weld. With the fusion welder, all you’re using is a laser to heat up the materials, and they just melt into each other.”
How is this different from conventional welding? Laviano replies, “Conventional welding can be a very slow process and not very consistent regardless of how good a welder can be. With the robotic welders, you can get an excellent, consistent weld. You can use it as part of the manufacturing process repetitively and expect the same results every time.”
Hugo Arias, Boyce Technologies Machinist, agrees, “the new equipment opens a lot of doors for a lot of innovations, especially the laser welders. The TRUMPF 5020 Robotic Laser Welder helps because it hides the weld, you don’t get the traditional weld that you have to clean up. We can now have a seam weld, and all you see is a tiny line – the size of a pen mark!”
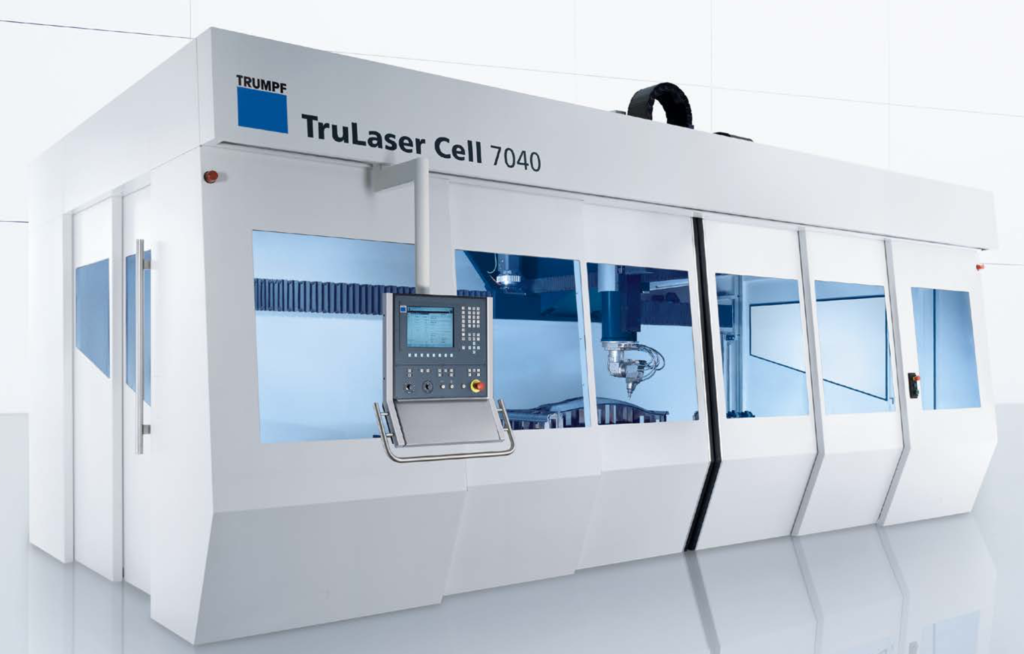
The TRUMPF 7040 Robotic Laser Cell is setting a new standard in terms of speed and production efficiency. This new fiber technology allows the laser light cable for both welding and cutting operations. To switch from cutting to welding or vice versa, it is merely necessary to replace the processing optics – the system controls will automatically adjust the output. The TRUMPF 7040 is highly versatile and provides optimal processing results for two- or three-dimensional components.
Superior sheet metal cutting and bending
The TRUMPF 2030 Trulaser Cutter, the TRUMPF 7040 Trulaser Cell, and the TRUMPF 3100 Trubend Hydraulic Brake have revolutionized Boyce Technologies sheet metal manufacturing system. The TRUMPF 2030 Trulaser Cutter, using a four-kilowatt laser, provides high cutting productivity with minimal downtimes. The TRUMPF 7040 Trulaser Cell, in addition to welding, offers even higher cutting speeds due to its 6000-watt laser power and ability to change sheets within seconds. The Trubend Hydraulic Brake, with a 100-ton capacity, creates highly accurate and repeatable results in bending steel and aluminum sheet metal.
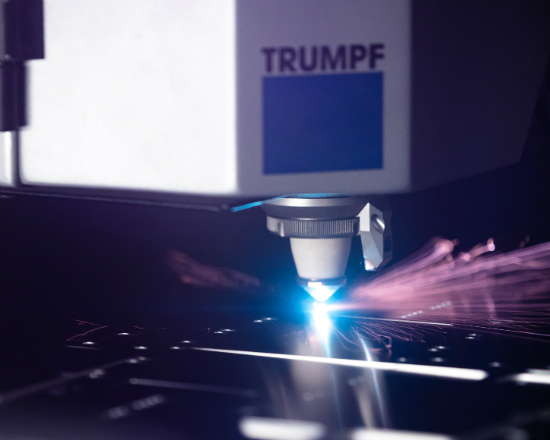
Brandon Ye, Mechanical Engineer at the R&D Department, oversees the sheet metal operations. In explaining the process, Ye shares “Charles (Boyce) will conceptualize an idea and tell me what needs to be made, and show me a 2D image and explain how it should work. From there, I create a 3D model and use it to program how to cut and it in real life in sheet metal. The rest is magic.”
The laser cutter and hydraulic brake has been invaluable in prototyping and creating next generation Boyce Technologies products. “It has a been a privilege to operate on these machines, and it’s fun to watch how they cut metal like paper. You then pull out the product and say ‘Wow!’, it is very fulfilling! When you see something you conceptualized in your mind, then programmed into a computer, and then created into real life – that is what I like,” says Ye.
Streamlined Advanced Manufacturing Processes
A great benefit of these new capabilities to our customers is that we can now eliminate the middleman, and streamline our manufacturing. “Every new piece of equipment brings new options to us, and also increases the speed at what we get to do and design and prototype,” says Laviano. “There are things that we had to wait for outsourcing, which was a big problem. There were things that we couldn’t do in-house that we would have loved to do. Heat sinks and exchangers are things we like to do a lot because building our thermal management systems for a custom chassis is great, so the robotic laser welders are going to be a great addition for welding copper to aluminum. Cutting things much quicker and precise with the laser is extremely useful. We want to build things that are much smaller, much more compact, perform better and much more unique to the consumer.”
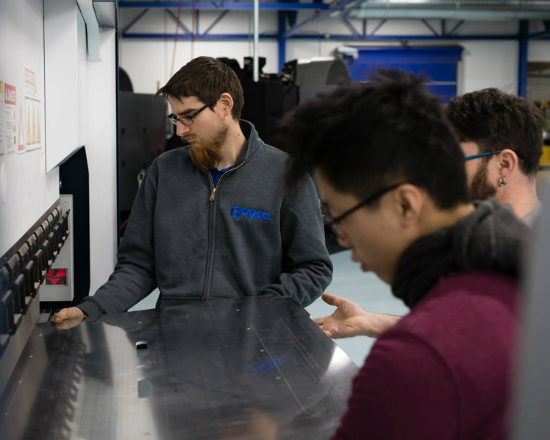
Laviano continues, “The ability to bend our metal in-house is amazing. Normally, we’re not big fans of bending materials, as we worry about consistency and the look of it. However, after using the TRUMPF 3100 Trubend Hydraulic Brake and seeing the consistency, we’re falling in love with it. The machinery allows us to continue to push for more creativity, our engineering boundaries, and defy physics. The limitations now are no longer due to tools, but more from the imagination of the engineering team and everyone who’s involved.”
New Advanced Manufacturing Machines, Unlimited Possibilities
What is it like to be able to create new innovative products at a faster and efficient pace? “These machines have exceeded my expectations. Charles has given me an opportunity for learning all this new technology, and I’m beyond excited,” says Hugo Arias. “Everyday, I’m learning something new. I love coming to work!”
“I’d say it’s like living a big kid’s dream, where you get to play with all the toys and make something and see it grow in front of you, and get hands-on,” says Laviano. “The best part is that it is not the same redundant thing every day. We do things that are not too far away from your comfort zone, but just enough so you’re excited to learn it.” The Boyce team works passionately to create advanced manufacturing solutions for our customers. We will continue to be on the forefront of advanced engineering and manufacturing. We’re thrilled about our new additions, and we’re ready to work for you.
To learn more about Boyce Technologies advanced manufacturing solutions, please contact us or call 212-385-8585
[gravityform id=”3″ title=”true” description=”true”]